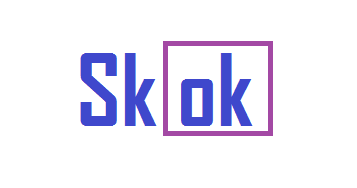
Best Practices for Quality Control
Structural Foam Injection Molding has become an essential technique in modern manufacturing, particularly when producing large, durable, and lightweight plastic components. This process involves injecting a foaming agent along with plastic resin into a mold, which results in a cellular core surrounded by a solid outer layer. While the method offers numerous advantages such as material savings, strength, and weight reduction, ensuring quality control throughout the manufacturing cycle is critical for product performance and customer satisfaction. To maintain consistent quality, manufacturers must adopt and implement rigorous quality control practices tailored specifically for Structural Foam Injection Molding.
This article explores the best practices for quality control in Structural Foam Injection Molding, from material selection to post-production inspection. By understanding and implementing these practices, manufacturers can improve efficiency, reduce waste, and maintain high-quality standards in every molded product. Let’s dive into the crucial elements that contribute to quality assurance in this specialized molding technique.
Material Selection and Preparation
Quality control in Structural Foam Injection Molding starts with choosing the right raw materials. Selecting high-grade thermoplastics and compatible chemical blowing agents is critical for achieving the desired cell structure and mechanical properties in the final product. Materials such as polyethylene, polypropylene, and ABS are commonly used for their compatibility with foaming agents and structural performance. Inconsistent or contaminated materials can result in uneven cell formation, poor surface finish, or compromised strength. Therefore, sourcing from reputable suppliers and ensuring proper documentation for each batch is a vital first step.
Equally important is the preparation of these materials before they are used in the molding process. Moisture content in plastic pellets must be closely monitored and controlled, as excessive moisture can cause voids, splay, or weak bonding in the molded part. Implementing proper drying procedures and using moisture analyzers can ensure that materials are processed in optimal condition. Monitoring the blend ratios of resin and blowing agents also helps maintain consistent foam density, directly affecting the part’s structural integrity and surface quality.
Process Monitoring and Control
Effective process control is essential in Structural Foam Injection Molding to maintain consistency and minimize defects. Since the process involves a chemical reaction that generates gas within the mold, maintaining the correct temperature and pressure is crucial. Variations in these parameters can lead to improper foaming, warping, or incomplete filling of the mold. Utilizing real-time monitoring systems to track variables such as injection speed, mold temperature, and holding pressure helps in maintaining optimal processing conditions.
Advanced process control software and automated molding machines can greatly enhance quality control by providing precision and repeatability. Data logging and analytics allow operators to detect trends or anomalies early in the production cycle. This real-time feedback enables rapid adjustments, minimizing scrap and downtime. Implementing closed-loop control systems that adjust processing conditions automatically based on feedback from sensors can lead to improved product quality and greater process stability, especially when working with complex part geometries.
Mold Design and Maintenance
The design of the mold plays a significant role in ensuring quality in Structural Foam Injection Molding. A well-designed mold facilitates uniform foam distribution and ensures that the part maintains its structural integrity and surface appearance. Key design considerations include balanced gating systems, proper venting, and sufficient wall thickness to accommodate the expanding foam. Computational simulations during the design phase can predict potential flow issues and allow engineers to refine the mold before production begins.
Regular maintenance of the mold is equally important to prevent defects and prolong the mold’s lifespan. Over time, residue buildup from the foaming agents or wear and tear on mold surfaces can affect part quality. A preventative maintenance schedule that includes mold cleaning, inspection, and polishing helps maintain dimensional accuracy and reduces the risk of flash, incomplete filling, or ejection problems. Maintaining mold temperature control systems is also essential for consistent foam expansion and product quality.
In-Process Quality Inspection
Implementing in-process quality inspection techniques is a proactive way to detect and correct issues before they result in significant defects or material waste. Visual inspection is the most basic and widely used method, allowing operators to spot surface defects, warpage, or short shots as soon as parts are ejected from the mold. However, more advanced inspection techniques can provide deeper insights into the internal structure and performance characteristics of foam-molded parts.
Techniques such as ultrasonic testing, X-ray inspection, and density analysis can be used to verify the consistency of the cellular structure within the molded component. By evaluating the internal composition of the part, manufacturers can ensure that the foaming process occurred uniformly, providing the necessary strength-to-weight ratio. Using statistical process control (SPC) tools, quality inspectors can track performance metrics over time, enabling early detection of deviations and continuous improvement of the molding process.
Final Testing and Documentation
The final stage in the quality control process for Structural Foam Injection Molding involves comprehensive product testing and documentation. Depending on the application, parts may undergo mechanical testing such as tensile strength, flexural modulus, impact resistance, and load-bearing capacity. These tests verify that the components meet functional requirements and are suitable for their intended use. For critical applications such as automotive, aerospace, or medical devices, parts must also comply with specific industry standards and certifications.
In addition to physical testing, maintaining detailed records of the molding process, material batches, and inspection results is crucial for traceability and regulatory compliance. Documentation helps in identifying the root cause of any quality issues and supports continuous improvement initiatives. A robust quality management system (QMS), such as ISO 9001, ensures that all processes are documented, monitored, and audited regularly. This systematic approach not only enhances product quality but also strengthens customer trust and satisfaction.
Conclusion
Structural Foam Injection Molding offers many advantages for producing lightweight yet strong components across various industries. However, without a robust quality control system in place, manufacturers may face issues such as inconsistent foaming, poor structural performance, or product failures. By adopting best practices in material selection, process control, mold design, in-process inspection, and final testing, manufacturers can significantly reduce defects and deliver superior products.
Quality assurance in Structural Foam Injection Molding is not a one-time effort but an ongoing commitment to excellence. Leveraging advanced technologies, adhering to industry standards, and training personnel in quality best practices can make a substantial difference in the outcome of the manufacturing process. In an increasingly competitive market, high-quality production not only sets a business apart but also ensures long-term success.