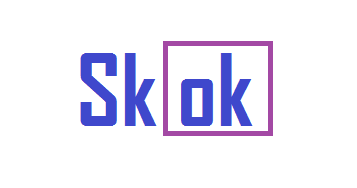
Quality Prototype Injection Molding
In the fast-paced world of product development, getting from concept to market quickly and efficiently is crucial. One of the most effective ways to streamline this process is through quality prototype injection molding. This manufacturing technique allows designers and engineers to create precise prototypes of their products, enabling them to test and validate designs before committing to full-scale production. By using quality prototype injection molding, companies can identify potential issues early in the development process, saving time and money while ensuring that the final product meets customer expectations.
In this article, we will explore what prototype injection molding is, the steps involved, the advantages it offers, and how it has become a vital part of product development across various industries.
What Is Prototype Injection Molding?
Prototype injection molding is a manufacturing process used to produce plastic parts by injecting molten plastic into a mold. Unlike traditional mass production injection molding, prototype injection molding is typically used to create small quantities of parts to evaluate and test design concepts. The primary goal of prototype injection molding is to produce parts that closely resemble the final product, allowing for functional testing, fit checks, and performance evaluations.
The process is highly beneficial during the product development phase because it enables designers to test and refine their designs quickly and cost-effectively before committing to full-scale production. Prototype injection molding is often used for producing functional prototypes, visual prototypes, or pre-production samples that will be tested under real-world conditions.
The Prototype Injection Molding Process
The prototype injection molding process involves several critical steps, each ensuring that the final part meets the design specifications and functional requirements. Let’s break down the key stages of the process:
1. Design and CAD Modeling
The first step in prototype injection molding is designing the part. Engineers and product designers create a 3D model of the part using Computer-Aided Design (CAD) software. The design must be optimized for both functionality and manufacturability, considering factors such as material choice, part geometry, and moldability.
Once the design is completed, it is crucial to simulate how the molten plastic will flow through the mold and ensure that the part can be successfully molded without defects. This stage often includes making adjustments to the design to avoid issues like warping, air bubbles, or uneven filling.
2. Creating the Mold
The next step is to create the prototype mold. Since this is a prototype, the mold is typically made from less expensive materials such as aluminum or steel, which allows for faster production at a lower cost compared to molds used for mass production. The mold is manufactured based on the 3D CAD model, and its cavities are precisely shaped to match the desired part.
The mold is critical to the success of the injection molding process, as it must accurately replicate the part design and be able to withstand the high pressures and temperatures required during molding.
3. Injection Molding
Once the mold is ready, the next step is to inject molten plastic into it. In the injection molding machine, plastic pellets are heated to a liquid state and injected into the mold cavity at high pressure. The plastic then cools and solidifies inside the mold, taking the shape of the desired part.
The machine applies pressure to ensure that the mold is completely filled, and once the part has cooled, it is ejected from the mold. This step may involve several iterations to ensure that the part meets the desired specifications and quality standards.
4. Post-Processing
After the prototype parts are molded, post-processing may be required to refine the parts further. This can include removing excess plastic (also known as flash), trimming, polishing, or adding surface finishes. Depending on the specific application, additional processes like painting, coating, or assembly may also be performed.
The purpose of post-processing is to ensure that the prototype part is as close to the final product as possible, allowing for realistic testing and evaluation.
5. Testing and Evaluation
Once the prototypes are produced, they undergo rigorous testing and evaluation to determine if they meet the desired functionality and performance standards. This testing phase is crucial, as it helps identify any design flaws, material issues, or manufacturing problems that could impact the final product’s performance.
Depending on the product, testing can include things like stress tests, fit tests, environmental simulations, and durability assessments. The results from this phase may lead to design modifications, further prototypes, or adjustments to the molding process.
6. Feedback and Iteration
Once the prototypes are tested and evaluated, feedback is gathered to assess the part’s performance. Based on the feedback, adjustments can be made to the design, material selection, or mold construction. The iterative nature of prototype injection molding allows designers to continuously improve the part until it meets all specifications and is ready for mass production.
Advantages of Quality Prototype Injection Molding
Prototype injection molding offers numerous benefits that make it an ideal choice for companies looking to develop and test new products. Some of the key advantages include:
1. Faster Time to Market
Using prototype injection molding allows designers and engineers to create functional prototypes quickly and efficiently. The ability to test prototypes early in the design process helps identify potential issues and correct them before full-scale production begins. This reduces the risk of delays and ensures that the product reaches the market faster.
2. Cost-Effective Testing
Prototype injection molding is much more affordable than traditional low-volume manufacturing techniques, particularly for producing functional parts. Since only small quantities are produced, companies can conduct thorough testing without committing to the higher costs of mass production. It also reduces the need for costly revisions later in the process.
3. High-Quality Prototypes
Prototype injection molding produces parts with high precision and excellent surface finishes. The process allows for the creation of highly detailed and accurate prototypes that mimic the final product, making it easier to evaluate the design’s functionality and aesthetics. This level of quality is essential for industries where performance and reliability are paramount.
4. Material Versatility
With prototype injection molding, manufacturers can use a wide range of materials, from standard plastics like ABS and polycarbonate to specialized materials such as high-temperature plastics or composites. This flexibility enables companies to test prototypes with materials that closely resemble the final product’s material, ensuring a more accurate evaluation.
5. Design Flexibility
Prototype injection molding allows for rapid iteration of designs, enabling designers to make changes and improvements as needed. The ability to create and test multiple iterations of a product in a short amount of time helps companies optimize their designs and avoid costly mistakes later in the production process.
6. Realistic Testing and Validation
By using prototype injection molding, companies can test prototypes under real-world conditions. This provides valuable insights into how the part will perform in the final product and ensures that any potential design flaws are identified and addressed before mass production begins.
7. Low Volume Production
Prototype injection molding is ideal for low-volume production, making it a cost-effective solution for creating small batches of parts for testing or pre-production purposes. This is especially beneficial for startups or companies developing products that do not require large-scale manufacturing.
Applications of Prototype Injection Molding
Prototype injection molding is widely used across various industries to develop and test new products. Some common applications include:
1. Automotive
The automotive industry uses prototype injection molding to develop and test components such as dashboards, housing units, and interior parts. By producing functional prototypes, manufacturers can test fit, finish, and performance before moving to large-scale production.
2. Consumer Electronics
In the consumer electronics industry, prototype injection molding is used to create prototypes of housings, connectors, and other components. It allows manufacturers to evaluate the design, ergonomics, and functionality of electronic devices before mass production.
3. Medical Devices
Medical device manufacturers rely on prototype injection molding to develop precise and functional prototypes of components like surgical tools, implants, and diagnostic devices. The high level of accuracy and material flexibility allows for rigorous testing and validation.
4. Aerospace
In the aerospace industry, prototype injection molding is used to create parts such as brackets, housings, and fittings that must meet strict quality and performance standards. Prototypes are thoroughly tested to ensure they meet safety and durability requirements.
5. Consumer Goods
From household products to toys and sporting equipment, prototype injection molding is used to test the design and functionality of consumer goods before they enter the mass market. Prototypes help identify potential improvements in design and materials.
Conclusion
Quality prototype injection molding is a crucial part of the product development process, allowing manufacturers to create precise, functional prototypes quickly and affordably. This process enables companies to test designs, evaluate materials, and make necessary adjustments before moving into full-scale production, ultimately saving time and costs. The flexibility, precision, and versatility of prototype injection molding make it an invaluable tool for industries such as automotive, aerospace, medical devices, and consumer electronics. As product development continues to evolve, prototype injection molding will remain a key technology in ensuring that the final products meet customer expectations and perform flawlessly.