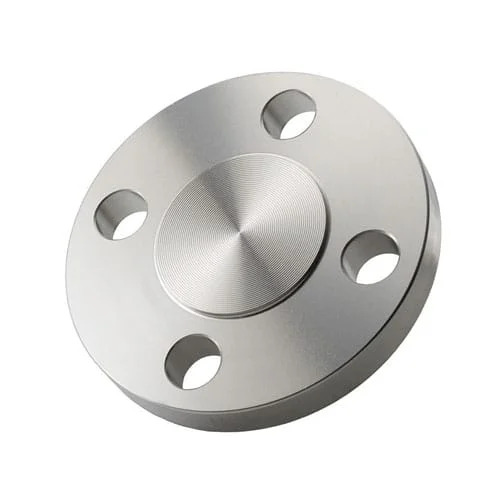
Why Blind Flanges Are Vital in Shut
In the world of piping systems and industrial applications, a blind flange is an essential component used to seal the end of a pipe, valve, or other types of piping systems. The role of blind flanges in shut-off applications is often underestimated, but these flanges are incredibly important in preventing leakage, ensuring safety, and maintaining the efficiency of various systems. Whether you’re dealing with high-pressure environments, corrosive chemicals, or simply the need for secure isolation, blind flanges are crucial for optimal performance.
What Are Blind Flanges?
A blind flange is a flat, circular disc used to seal the end of a pipe, valve, or other piping equipment, preventing the flow of fluid or gas. Unlike standard flanges, which connect two sections of pipe, a blind flange serves only to close or seal a section of piping. It is essentially “blind” because it does not have any opening for flow.
This component is typically used in situations where future access to the piping system might be needed, but where there is no immediate need for fluid to flow through. Blind flanges are used for maintenance purposes, temporary shut-off, or in situations where a permanent seal is needed until further action can be taken.
Why Are Blind Flanges Essential in Shut-Off Applications?
Blind flanges serve as the most secure way to completely block off a section of piping in various industries. They are vital in shut-off applications for several reasons. Here’s a breakdown of why blind flanges are so essential:
1. Preventing Leaks and Ensuring Safety
The primary function of a blind flange is to create a leak-proof seal, ensuring that no fluids or gases escape from the closed section of the pipeline. In any piping system, leaks can be dangerous, leading to potential environmental harm, loss of product, or even catastrophic accidents. Blind flanges eliminate the risk of such leaks by securely sealing the end of a pipe, ensuring safety for operators and the surrounding environment.
2. Temporary and Permanent Shutdowns
In many industrial applications, equipment needs to be temporarily shut down for maintenance, inspection, or repairs. During these times, a blind flange is used to block off sections of piping that are not in use. This ensures that the rest of the system can continue operating while specific sections are safely isolated. When maintenance is complete, the blind flange can be removed or replaced, allowing the system to resume normal operations.
3. Facilitating System Modifications
In some situations, piping systems need to be modified or updated. A blind flange provides a quick and easy way to isolate certain sections of a pipeline, enabling technicians to make adjustments without disturbing the entire system. Whether you’re adding new piping, replacing old components, or expanding your system, blind flanges help in these modification tasks.
4. Meeting Regulatory Compliance
Certain industries, such as oil and gas, chemical processing, and nuclear power, require strict adherence to safety and operational standards. The use of blind flanges helps ensure compliance with these standards by maintaining leak-proof seals and preventing hazardous conditions that could arise from faulty connections.
5. Cost-Effective Solution for Shut-Off Applications
Using a blind flange is often more cost-effective than installing a valve or other complex shut-off devices, especially in cases where the shut-off is only temporary. These flanges are straightforward in design and easy to install and remove, which reduces labor costs and system downtime.
Types of Blind Flanges
Blind flanges come in various designs, materials, and sizes to accommodate different applications. Below are some of the common types of blind flanges:
1. Weld Neck Blind Flange
Weld neck blind flanges are one of the most common types of blind flanges used in shut-off applications. These flanges are welded directly onto the end of the pipe, providing a strong and secure connection. The tapered design of the weld neck makes this flange ideal for high-pressure applications, as it can withstand the internal stresses of the system.
2. Slip-On Blind Flange
Slip-on blind flanges are simpler to install than weld neck flanges. These flanges slip over the end of the pipe and are then bolted into place. While not as robust as weld neck flanges, they are still commonly used for shut-off applications where pressure and stress are not as high.
3. Blind Flange with Raised Face
The raised face blind flange is similar to a standard blind flange, but with a raised section in the center. This raised face helps to create a better seal when used with a gasket, making it ideal for applications that require a higher level of leak prevention.
4. Flat Face Blind Flange
A flat face blind flange is designed to be installed against a flat surface. These flanges are ideal for low-pressure systems where the risk of leakage is minimal. Flat face blind flanges are typically used in systems where the sealing requirements are not as stringent as in high-pressure or hazardous applications.
5. Ring-Type Joint Blind Flange
Ring-type joint blind flanges are designed to provide an exceptionally tight seal. They are commonly used in high-pressure applications where a high level of security is required. The sealing ring ensures that the flange provides a tight seal even under extreme conditions.
Applications of Blind Flanges
The use of blind flanges is widespread across various industries. Below are some of the main sectors that rely on these flanges for their shut-off applications:
1. Oil and Gas Industry
The oil and gas industry frequently uses blind flanges in pipeline systems to isolate sections of piping for maintenance or to prevent leakage in high-pressure conditions. These flanges are often used in offshore platforms, refineries, and pipelines to ensure safe operations in hazardous environments.
2. Chemical Processing
In chemical processing plants, blind flanges are used to prevent leaks of hazardous chemicals and gases. These flanges provide a secure and leak-proof seal that helps to avoid environmental contamination and health risks to workers. They are also used to isolate equipment during maintenance or system upgrades.
3. Water Treatment Plants
Water treatment plants use blind flanges to isolate sections of piping during repairs or modifications. These flanges are essential for ensuring that water treatment processes continue without disruption while certain sections of the system are temporarily shut off.
4. Pharmaceutical Industry
In pharmaceutical manufacturing, contamination can lead to significant product losses and regulatory issues. Blind flanges are used in piping systems to prevent the escape of chemicals and maintain the purity of the product. The secure shut-off capabilities of these flanges are essential in maintaining stringent quality control standards.
How to Choose the Right Blind Flange for Shut-Off Applications
Selecting the right blind flange for a shut-off application depends on various factors such as the type of fluid being handled, pressure, temperature, and the specific needs of the system. Below are some tips to help you choose the right blind flange:
1. Material Selection
The material of the blind flange must be compatible with the fluid being handled. Common materials for blind flanges include carbon steel, stainless steel, and alloy steel. For corrosive environments, a material such as stainless steel or special alloys may be required to resist rust and degradation.
2. Pressure and Temperature Ratings
Ensure that the blind flange you choose can withstand the pressure and temperature conditions of your system. High-pressure applications require stronger materials and designs, such as weld neck blind flanges, to ensure secure sealing.
3. Flange Size
The size of the blind flange must match the size of the pipe it is sealing. Ensure that the flange is designed to fit the pipe’s dimensions, including the diameter and thickness.
4. Sealing Mechanism
Consider the sealing mechanism of the flange, such as a gasket or ring-type joint, to ensure it provides a tight seal. The sealing mechanism plays a crucial role in preventing leaks in shut-off applications.
Conclusion
In conclusion, blind flanges are vital components in shut-off applications across various industries. They provide a safe, cost-effective, and reliable way to prevent leaks, isolate sections of piping, and ensure regulatory compliance. Whether used for temporary shutdowns, system modifications, or permanent seals, blind flanges are indispensable for maintaining the integrity and safety of piping systems. Understanding the types, applications, and selection criteria for blind flanges can help you choose the right solution for your specific needs.
For more information on blind flanges and other related products, visit our flanges product page.