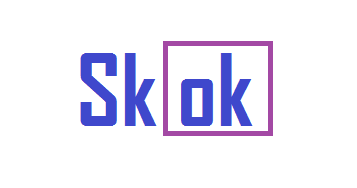
Why Die Casting Is Essential for Hi
Die casting is a manufacturing process that involves forcing molten metal into a mold cavity under high pressure. This technique is widely used for creating complex and precise metal components in various industries, including automotive, aerospace, electronics, and medical devices. The process ensures consistent quality, high production rates, and the ability to create intricate shapes that would be difficult or impossible with other manufacturing methods.
One of the key advantages of die casting is its ability to produce parts with tight tolerances and smooth surface finishes, eliminating the need for extensive post-processing. The use of non-ferrous metals such as aluminum, zinc, and magnesium makes die casting an ideal choice for applications requiring lightweight yet strong components. The combination of precision, efficiency, and cost-effectiveness makes die casting a preferred method for producing high-quality precision parts.
Advantages of Die Casting in Precision Manufacturing
Die casting offers several advantages over other metalworking processes, making it an essential technique for manufacturing precision parts. First, it enables high production efficiency by allowing for rapid cycle times and minimal material waste. Unlike traditional machining, which removes material from a solid block, die casting forms the final shape directly, significantly reducing material costs.
Additionally, die casting provides exceptional dimensional accuracy, ensuring that components meet strict specifications with minimal variations. This precision is crucial for industries that demand high-quality parts with consistent performance, such as aerospace and medical technology. The ability to achieve fine details and complex geometries without additional machining further enhances the appeal of die casting for precision manufacturing.
Applications of Die Casting in Various Industries
The versatility of die casting makes it a crucial manufacturing process in numerous industries. In the automotive sector, die-cast components are used in engine blocks, transmission cases, and structural parts due to their lightweight properties and durability. This contributes to improved fuel efficiency and overall vehicle performance.
In the electronics industry, die casting is utilized to produce intricate housings and heat sinks for devices such as smartphones, laptops, and LED lighting. The superior thermal conductivity of die-cast materials helps in heat dissipation, ensuring the longevity and reliability of electronic components. Other industries, including aerospace and medical, also rely on die casting to produce high-precision, high-strength components that meet stringent safety and performance standards.
The Role of Advanced Die Casting Technologies
Modern die casting has evolved significantly with the integration of advanced technologies such as computer-aided design (CAD), automation, and real-time monitoring. These innovations have enhanced the accuracy, speed, and efficiency of die casting processes, making it possible to create even more precise and complex parts.
Automated die casting systems reduce human error and improve consistency, while real-time quality monitoring ensures that defects are detected and corrected during production. Additionally, the use of vacuum-assisted die casting and squeeze casting techniques has improved the strength and integrity of cast parts, further expanding the applications of die casting in high-performance industries.
Sustainability and Cost-Effectiveness of Die Casting
Die casting is not only efficient but also environmentally friendly and cost-effective. The ability to reuse and recycle metals such as aluminum and zinc significantly reduces material waste and production costs. This makes die casting a sustainable choice for manufacturers looking to minimize their environmental footprint while maintaining high-quality standards.
Furthermore, die casting minimizes the need for secondary machining and finishing processes, reducing labor and production expenses. The long tool life of die-casting molds also contributes to cost savings, making it a financially viable option for large-scale production. As industries continue to prioritize sustainability and efficiency, die casting remains an indispensable method for producing high-quality precision parts.
Conclusion
Die casting is a fundamental process in modern manufacturing, enabling the production of high-quality precision parts with exceptional accuracy, strength, and efficiency. Its applications span multiple industries, from automotive to aerospace, and the continuous advancements in technology further enhance its capabilities. With sustainability and cost-effectiveness in mind, die casting continues to be an essential method for producing reliable and high-performance components.